Unleashing Creativity with Screenprinting Inks: A Comprehensive Guide
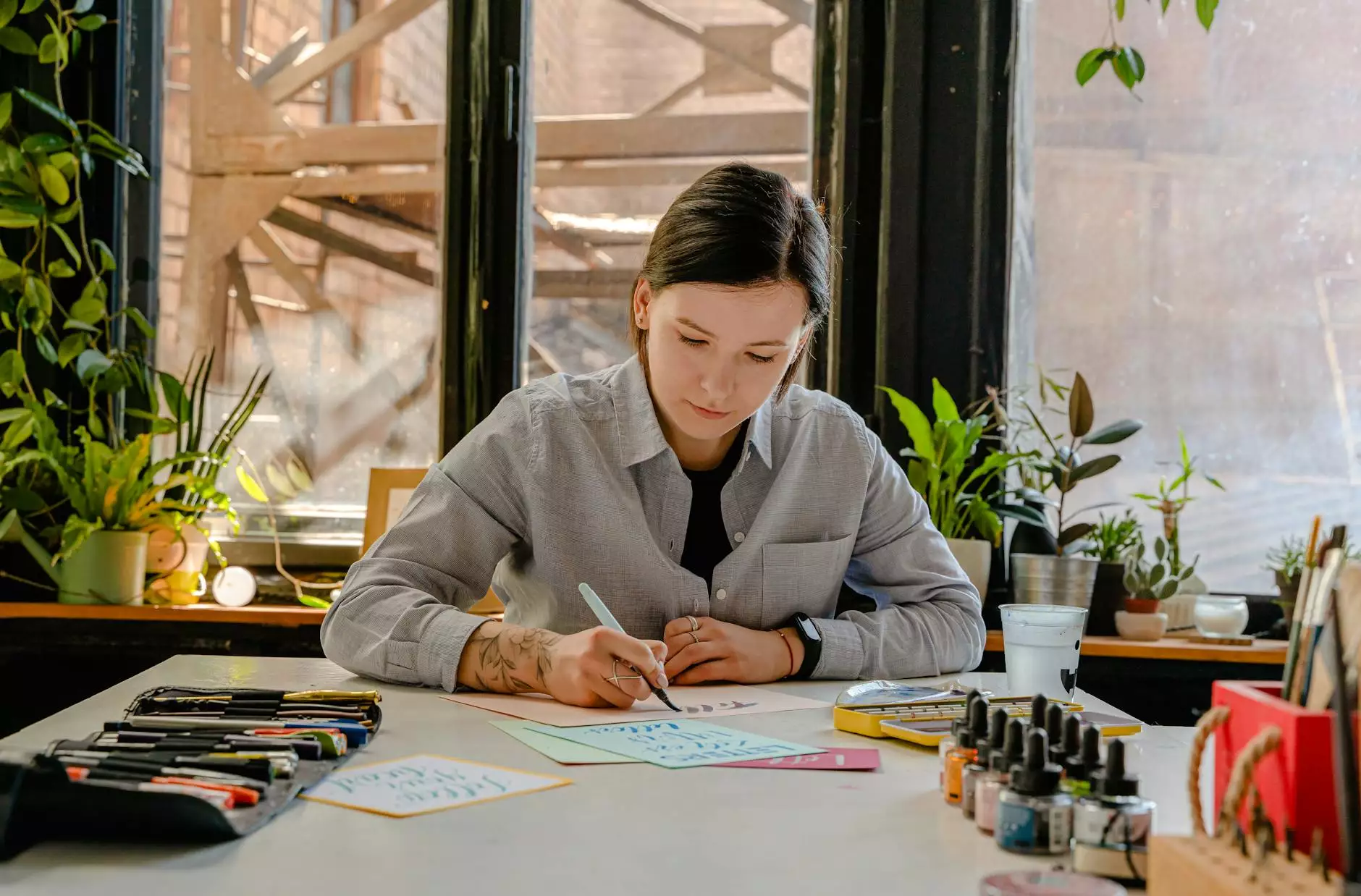
Screenprinting inks are a vital component in the field of printing services, paving the way for endless creativity and innovation in various industries. Understanding the diverse types and applications of these inks can significantly enhance both the quality of printed materials and the efficiency of printing processes. In this in-depth article, we will explore the various facets of screenprinting inks, their advantages, types, applications, and tips for selecting the right products for your printing needs, particularly focusing on how they can benefit businesses like Boston Industrial Solutions.
What are Screenprinting Inks?
Screenprinting inks are specially formulated inks used in the screen printing process. This printing technique involves forcing ink through a mesh screen stencil, allowing for detailed designs and vibrant colors to be transferred onto various surfaces. The unique qualities of screenprinting inks make them ideal for a wide range of applications, from textiles to promotional products.
The Evolution of Screenprinting Inks
The history of screenprinting inks dates back decades, initially utilizing oil-based inks for printing on fabric. Over the years, advancements in chemistry and technology have propelled the development of various ink types, catering to different materials and industrial needs. Today, screenprinting inks are formulated for performance, durability, and color vibrancy, significantly enhancing the output quality.
Types of Screenprinting Inks
Understanding the different types of screenprinting inks is crucial for achieving optimal results in your printing projects. Below are some of the most common categories:
1. Plastisol Inks
One of the most widely used types of screenprinting inks in the textile industry, plastisol inks are composed of polyvinyl chloride (PVC) particles suspended in a liquid plasticizer. They are known for:
- Vibrant Colors: Plastisol inks offer bright, opaque colors that remain consistent wash after wash.
- Durability: Once heat-cured, these inks create a solid bond with the fabric, resulting in long-lasting prints.
- Wide Range of Applications: Suitable for various fabrics, from cotton to polyester blends.
2. Water-Based Inks
Water-based inks are another popular choice in the screen printing world, especially for environmentally conscious businesses. Key benefits include:
- Eco-Friendly: These inks are made with water as a solvent, making them less harmful to the environment.
- Soft Hand Feel: Water-based inks penetrate the fabric fibers, resulting in prints that feel soft and natural.
- Excellent for Fine Detail: Water-based inks can produce high-resolution prints, particularly effective for detailed designs.
3. Solvent-Based Inks
Ideal for outdoor applications, solvent-based inks are known for their durability and weather resistance. Their advantages include:
- Longevity: These inks provide high resistance to fading and cracking, even under harsh environmental conditions.
- Versatility: Suitable for a wide variety of surfaces, including vinyl, plastics, and metal.
- High Color Saturation: Solvent-based inks produce rich, brilliant colors that stand out.
4. UV Inks
UV printing inks utilize ultraviolet light to cure or dry the ink instantly upon application. Their outstanding features include:
- Instant Drying: UV inks allow for immediate handling post-printing, enhancing production efficiency.
- High Gloss Finish: They provide a sleek, glossy finish that is particularly appealing for promotional materials.
- Durability: Resistant to fading and scratching, making them ideal for both indoor and outdoor applications.
Applications of Screenprinting Inks
The versatility of screenprinting inks allows them to be used across a myriad of applications. Here are some of the most common uses:
1. Textile Printing
Textile printing is one of the primary applications of screenprinting inks, especially in fashion and promotional apparel. Both plastisol and water-based inks are widely utilized due to their ability to produce high-quality, vibrant prints that withstand washing and wear.
2. Graphic Design and Artwork
Artists and graphic designers often use screenprinting inks to create limited-edition prints and decorative items. The ability to manipulate colors and layers allows for intricate and unique artwork.
3. Signage and Displays
Screenprinting inks are also popular in creating durable signs, banners, and displays. UV inks are particularly favored for outdoor signage due to their resistance to fading and weather elements.
4. Promotional Products
From mugs to bags and beyond, promotional products often utilize screenprinting techniques to showcase logos and branding. Solvent-based and UV inks are typically employed for these items to ensure longevity and visual appeal.
Choosing the Right Screenprinting Inks
With a plethora of screenprinting inks available, selecting the right type for your project can be challenging. Here are some factors to consider:
1. Material Compatibility
It is essential to choose inks that are compatible with the substrate you are printing on. For example, plastisol inks are ideal for cotton, while solvent-based inks excel on vinyl surfaces.
2. End Use
The intended use of the printed item plays a crucial role in ink selection. Consider whether the item will be used indoors or outdoors, how it will be laundered, and the level of wear it will endure.
3. Color and Finish
Depending on your design requirements, you may prefer inks with specific color qualities or finishes. For example, if a vibrant, glossy finish is desired, UV or solvent-based inks may be the right choice.
4. Environmental Considerations
If sustainability is a priority for your business, water-based inks are an eco-friendly option worth considering.
Conclusion: The Future of Screenprinting Inks
The use of screenprinting inks is set to evolve as industries become more focused on sustainability and technological advancements continue to unfold. Innovations in ink formulations, especially eco-friendly inks, are paving the way for greener practices in the printing services industry.
Boston Industrial Solutions, serving a diverse client base, can significantly benefit from integrating high-quality screenprinting inks into their offerings. By understanding the types, applications, and selection criteria of inks, businesses can ensure they meet their customers' needs effectively and sustainably.
FAQ about Screenprinting Inks
1. How do I properly clean screenprinting screens after use?
Thorough cleaning is essential for maintaining your screens. Use a suitable ink cleaner based on the type of ink used and ensure all residues are removed to preserve the screen's quality for future use.
2. Can screenprinting inks be mixed?
Mixing different types of screenprinting inks is often not recommended as they may have different curing properties, which can lead to print failures. It’s best to consult with the manufacturer for compatibility advice.
3. What is the best way to store screenprinting inks?
To prolong the life of your inks, store them in a cool, dry place away from direct sunlight. Ensure containers are sealed properly to prevent drying out or contamination.
4. Are there any health precautions I should take when using screenprinting inks?
Always use gloves and, if necessary, a mask when working with inks, especially solvent-based types, as they may emit harmful fumes. Ensure adequate ventilation in your workspace.