Unlocking Innovation with Ultem 1010: A Game-Changer in Product Design and 3D Printing
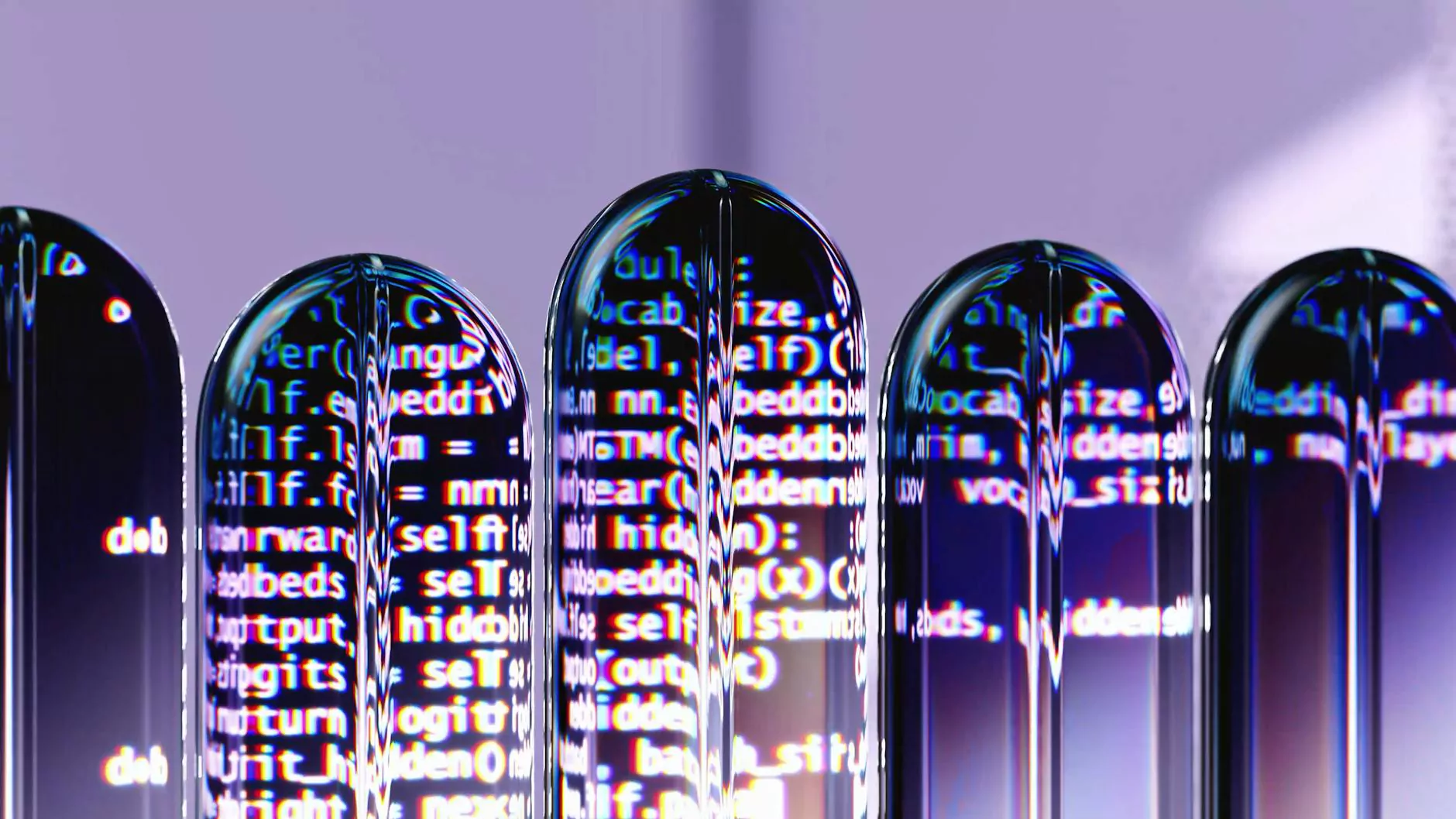
Ultem 1010 is not just a thermoplastic; it represents a significant advancement in the materials available for various industrial applications. This high-performance polymer, known for its impressive strength-to-weight ratio, thermal stability, and resistance to chemicals, is becoming the material of choice for engineers and designers alike. In a world where the demand for unique and functional designs is growing rapidly, understanding the advantages of Ultem 1010 can provide businesses with a competitive edge.
The Characteristics of Ultem 1010
Before diving into the applications of Ultem 1010, let’s explore its defining characteristics:
- High Strength: Ultem 1010 boasts excellent mechanical properties, making it suitable for applications where durability is crucial.
- Thermal Stability: With a high glass transition temperature (Tg), Ultem 1010 can perform well under extreme temperature conditions, maintaining its form and function.
- Chemical Resistance: This polymer exhibits strong resistance to various chemicals, including fuels, oils, and many solvents, which increases its versatility in application.
- Lightweight: The low density of this polymer allows for significant weight savings in product design, which can be essential in industries such as aerospace and automotive.
- Ease of Processing: Ultem 1010 can be easily processed through injection molding and 3D printing methods, facilitating innovative designs.
Applications of Ultem 1010 in Business
Thanks to its unique properties, Ultem 1010 is finding applications in various fields, transforming product design and manufacturing processes. Here are some of the most impactful uses:
1. Aerospace Industry
The aerospace industry demands materials that can withstand extreme conditions while being lightweight. Ultem 1010 meets these criteria, making it ideal for components such as:
- Electrical connectors
- Interior cabin components
- Thermal shields
These parts can endure high temperatures and stresses without compromising safety or performance.
2. Medical Devices
In the medical field, Ultem 1010’s biocompatibility and resistance to sterilization processes make it an excellent choice for:
- Surgical instruments
- Implants
- Prosthetics
The material’s durability ensures that devices perform reliably over extended periods, crucial for patient safety and efficacy.
3. Automotive Components
Automotive manufacturers are increasingly turning to Ultem 1010 for:
- Engine components
- Fuel system components
- Interior and exterior trim pieces
This polymer’s strength and lightweight nature contribute to higher fuel efficiency and enhanced vehicle performance.
4. 3D Printing and Prototyping
Ultem 1010 is particularly popular in the realm of 3D printing due to its:
- Versatility in creating complex geometries
- Ability to withstand rigorous testing
- High fidelity in reproducing intricate designs
Utilizing Ultem 1010 in 3D printing allows businesses to prototype rapidly and efficiently, reducing time-to-market and development costs.
The Importance of Ultem 1010 in Product Design
In product design, the choice of material can make or break a product's success. With Ultem 1010, designers are empowered to innovate while ensuring that their products meet the necessary performance requirements. Here are several reasons why Ultem 1010 is becoming indispensable in product design:
1. Design Flexibility
Ultem 1010 allows for a high degree of design flexibility, enabling the production of intricate shapes and configurations that may be impossible with traditional materials. This capability opens up new avenues for creativity in product development.
2. Cost Efficiency
While the initial costs of Ultem 1010 may be higher than other materials, the long-term savings are undeniable. Its durability means fewer replacements and repairs, leading to lower lifecycle costs.
3. Sustainability Considerations
As sustainability becomes a priority for many industries, the longevity and recyclability of Ultem 1010 play a critical role in reducing the overall environmental impact of products.
Challenges in Working with Ultem 1010
While the benefits of Ultem 1010 are numerous, it is essential to understand the challenges associated with its use:
1. Processing Challenges
Ultem 1010 requires specialized processing conditions to avoid issues such as warping or cracking during manufacturing. It is crucial for businesses to invest in the right equipment and training for their staff to maximize the potential of this material.
2. Cost Considerations
The upfront costs of Ultem 1010 can be a barrier for some businesses, particularly small startups. However, evaluating the long-term benefits can justify the investment.
Best Practices for Using Ultem 1010
To ensure the best results when working with Ultem 1010, consider the following best practices:
- Proper Preprocessing: Ensure that the material is dried thoroughly before processing to prevent moisture-related issues.
- Optimize Design: Take advantage of Ultem’s strength by designing parts that minimize weight while maximizing performance.
- Conduct Testing: It is vital to conduct rigorous testing on prototypes to understand the behavior of the material in real-world applications.
The Future of Ultem 1010 in Technology and Innovation
As technology continues to evolve, Ultem 1010 is poised to play a significant role in future innovations. Its application across various industries is likely to expand, especially in areas such as green technology, smart manufacturing, and advanced robotics.
The versatility and performance of Ultem 1010 make it an exciting material for developers seeking to push the boundaries of what is possible. By integrating this high-performance polymer into their designs, businesses can enhance their product offerings and meet the ever-growing consumer demand for quality, durability, and functionality.
Conclusion: Embracing Technology with Ultem 1010
In conclusion, Ultem 1010 stands as a testament to the ongoing quest for innovation in product design and manufacturing. Its exceptional properties provide businesses with the tools they need to create high-quality, reliable products that can compete in a global market.
By understanding the capabilities and applications of Ultem 1010, companies can leverage this material to optimize their processes and improve their product performance. As industries continue to evolve, those who embrace high-performance materials like Ultem 1010 will undoubtedly lead the way in technological advancements and sustainable practices.
For businesses keen on staying ahead in their respective fields—be it art supplies, product design, or 3D printing—integrating Ultem 1010 into their material palette is a strategic move that promises substantial returns.
Explore the endless possibilities with Ultem 1010 and revolutionize your approach to product development today!