Transforming Industries with **China Injection Molding**
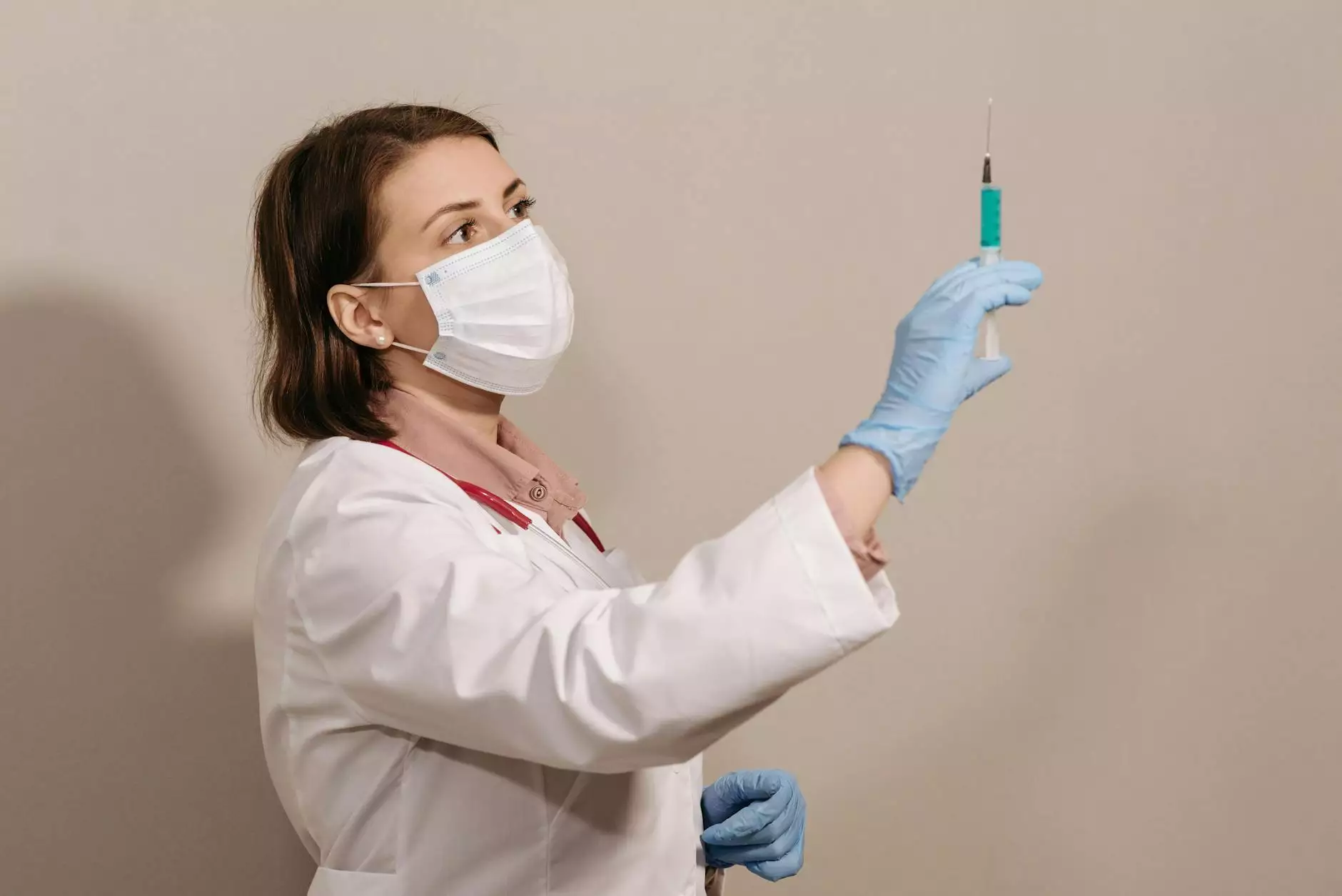
In the realm of modern manufacturing, few processes have demonstrated the capability to revolutionize efficiency and product excellence like China injection molding. This technique has become a cornerstone for businesses aiming to stay ahead in a highly competitive landscape. With manufacturers worldwide recognizing its profound benefits, it's crucial to understand what injection molding entails, especially its unique manifestations in China.
What is Injection Molding?
Injection molding is a manufacturing process for producing parts by injecting molten material into a mold. The process is widely used for making plastic products, but it can also apply to metals, glass, and other materials. Here’s how it works:
- Preparation of the Mold: An injection mold is crafted, typically from steel or aluminum. This mold consists of two halves—a core and a cavity that determines the final shape of the product.
- Injection Phase: The raw material is heated until it becomes molten and injected into the mold under high pressure.
- Cooling: The molten material cools and solidifies into the desired shape within the mold.
- ejection: The mold is opened, and the finished product is ejected.
The Rise of China Injection Molding in Global Manufacturing
China has emerged as a powerhouse in the field of injection molding, making it the go-to destination for companies worldwide that seek high-quality manufacturing at competitive prices.
1. High-Quality Standards
Chinese manufacturers have made significant advancements in technology and quality control processes. As a result, they can deliver injection molded products that meet international standards, ensuring durability and reliability across various applications.
2. Cost-Effectiveness
One of the most appealing aspects of China injection molding is its cost-effectiveness. The low labor costs, combined with large-scale production capabilities, result in significantly lower production expenses. This, in turn, allows businesses to optimize their budgets without compromising on quality.
3. Rapid Prototyping and Time Efficiency
With advanced technology and machinery, Chinese manufacturers can produce prototypes quickly through injection molding. This speed in development enables companies to accelerate their product launch processes, providing a competitive edge in the marketplace.
The Advantages of China Injection Molding
Choosing China injection molding comes with a multitude of advantages:
- Versatility: Injection molding is suitable for various materials, including plastics, metals, and composites.
- Consistency: This method provides excellent uniformity across batches, which is crucial for mass production.
- Complex Designs: Molds can be designed with intricate details, allowing for complex shapes that may not be achievable through other manufacturing methods.
Applications of China Injection Molding Across Industries
The applications of injection molding are virtually limitless, impacting diverse sectors such as:
1. Consumer Electronics
From smartphone cases to interior components, China injection molding plays a pivotal role in the production of consumer electronics. The precision offered by this manufacturing process ensures that components fit perfectly, leading to enhanced functionality.
2. Automotive Industry
The automotive sector benefits remarkably from injection molding. Components like dashboards, bumpers, and interior fittings are commonly produced using this technique, offering durability and lightweight characteristics.
3. Medical Devices
In the field of healthcare, injection molding is crucial for manufacturing various devices. The stringent quality standards in this industry make China injection molding an ideal choice due to its reliability and precision.
Understanding the Process of China Injection Molding
To appreciate how china injection molding works, it’s important to delve into its detailed stages:
1. Material Selection
The choice of material is essential, as it determines the properties of the final product. Common materials used include:
- Thermoplastics: Such as ABS, polystyrene, and polypropylene, which are ideal for their moldability and durability.
- Thermosetting Plastics: Such as unsaturated polyesters, which offer additional strength.
- Metals: Injected metals like aluminum are gaining traction for high-performance applications.
2. Injection Molding Machine Components
The machinery involved in China injection molding consists of several key components:
- Hopper: Where the raw material is fed into the machine.
- Injection Unit: Melts and injects the material into the mold.
- Mold: The heart of the process, where the shape is formed.
- Clamping Unit: Holds the mold halves together during the injection process.
3. Quality Assurance
Quality assurance is paramount in China injection molding. Procedures such as dimensional inspection, visual inspection, and functional testing are conducted to ensure that the products meet the specified requirements.
Choosing the Right Partner for China Injection Molding
With numerous manufacturers in China establishing a foothold in the injection molding industry, selecting the right partner is critical. Here are essential factors to consider:
1. Experience and Expertise
Assess the manufacturer's years in the business and their specialization in your required sector. Experienced manufacturers are more likely to understand the nuances of your product needs.
2. Technological Advancements
Ensure that the manufacturer employs the latest technologies in their production processes. This includes investing in modern machinery and adhering to advanced quality control standards.
3. Communication
Open and transparent communication is vital for project success. The ability of the manufacturing partner to understand your requirements and provide timely updates can save you from potential setbacks.
Sustainability in China Injection Molding
As global consciousness shifts towards sustainability, the injection molding industry is evolving as well. Many manufacturers in China are adopting eco-friendly practices, such as using biodegradable materials and integrating energy-efficient machinery.
1. Use of Recyclable Materials
Incorporating recyclable materials in production processes reduces waste and environmental impact. Additionally, many businesses are now exploring the use of recycled plastics in injection molding.
2. Energy Efficiency
By utilizing energy-efficient machinery, manufacturers can significantly lower their energy consumption during the injection molding process, contributing to a reduced carbon footprint.
Future Trends in China Injection Molding
The future of China injection molding holds exciting possibilities driven by innovation and technological advances:
1. Automation and Robotics
The integration of automation and robotics is set to enhance productivity and reduce labor costs further. Automated systems can operate machines faster and with greater accuracy.
2. 3D Printing Integration
Innovations are leading to the integration of 3D printing with injection molding. This combination allows for rapid prototyping and the production of customized molds, therefore reducing lead times.
3. New Material Development
Research into advanced materials such as composites will lead to stronger, lighter, and more durable products. Manufacturers who invest in these materials will find themselves at the forefront of the industry.
Conclusion: The Integral Role of China Injection Molding in Business Growth
In conclusion, China injection molding stands as a transformative force across various industries. With its remarkable advantages—cost efficiency, versatility, and rapid production capabilities—it remains an indispensable component of modern manufacturing. As companies seek to innovate and compete on a global scale, understanding and leveraging the capabilities offered by China injection molding will be increasingly vital for sustained growth and success.
For businesses interested in optimizing their manufacturing processes, working with reputable manufacturers can lead to exceptional outcomes. As a leading expert in injection molding, Deep Mould is committed to providing high-quality solutions that propel your business forward. Explore more about our services and how we can assist you at DeepMould.net.