Mastering Rapid Prototyping Injection Moulding for Metal Fabricators
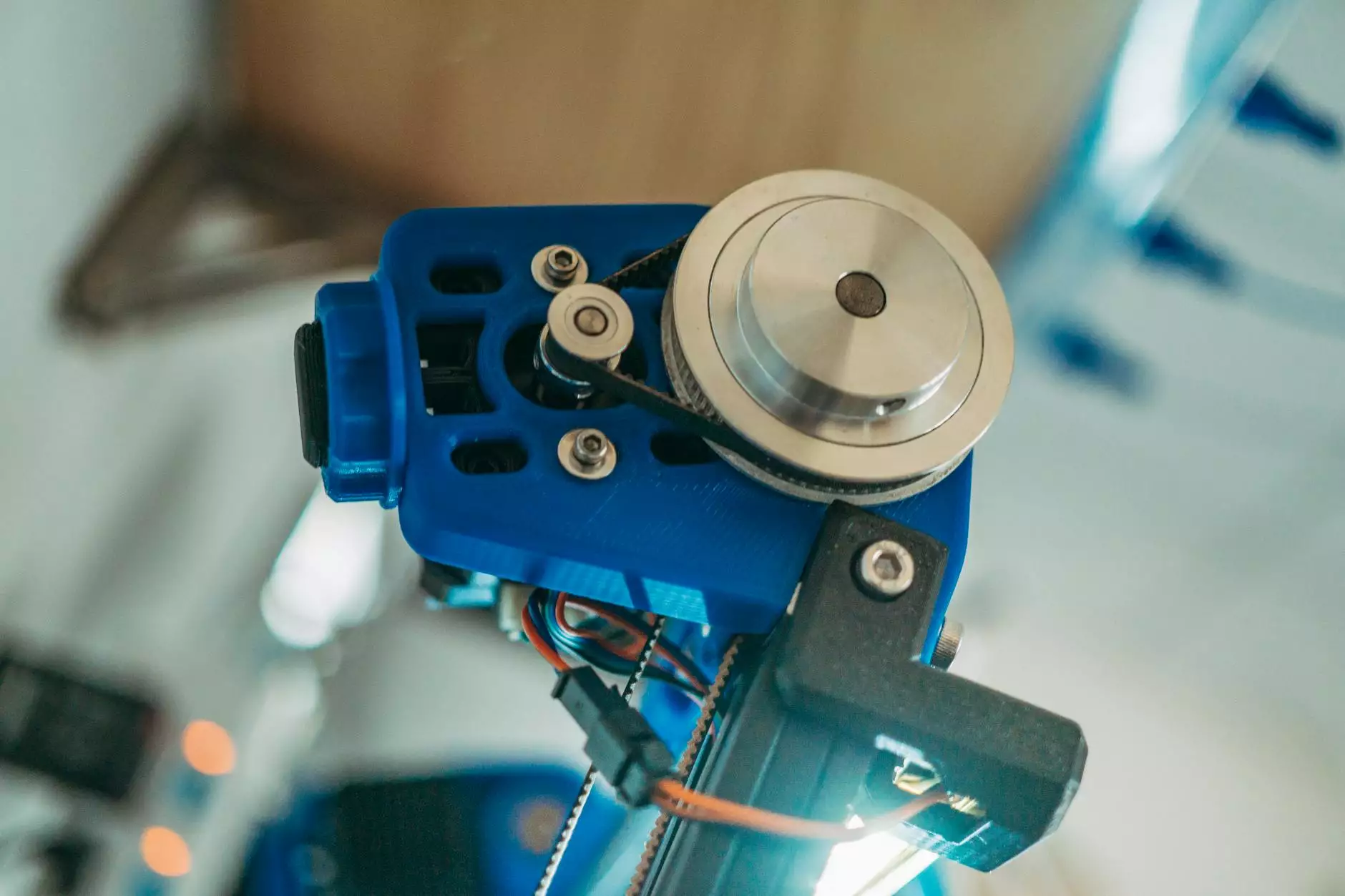
Rapid prototyping injection moulding has revolutionized the manufacturing landscape, especially for metal fabricators. This modern technique allows businesses to design and produce complex parts with speed and precision. As a staple for innovation, understanding its nuances can translate into significant advantages for any manufacturing company.
What is Rapid Prototyping Injection Moulding?
At its core, rapid prototyping injection moulding is the process of creating prototypes quickly and efficiently using injection moulding techniques. This method involves producing a mold where molten material, commonly thermoplastics and metals, is injected under pressure to shape parts. The speed of prototyping enables designers and engineers to test and refine products at a much quicker pace than traditional methods.
Why Choose Rapid Prototyping Injection Moulding?
Here are some compelling reasons to adopt rapid prototyping injection moulding in your metal fabrication processes:
- Accelerated Time-to-Market: The ability to produce prototypes swiftly allows businesses to bring products to market faster, enabling them to respond to customer needs and market demands promptly.
- Cost Efficiency: By minimizing waste and optimizing material usage, companies can significantly reduce costs associated with product development.
- Design Flexibility: Rapid prototyping encourages creative exploration of designs without the fear of incurring excessive costs for modifications.
- Enhanced Quality: More frequent testing and iteration improve the overall quality of the final product. Issues can be identified and rectified before mass production.
- Innovation Potential: With rapid prototyping, businesses can experiment with complex geometries and innovative designs that would be challenging with traditional methods.
How Does Rapid Prototyping Injection Moulding Work?
The process of rapid prototyping injection moulding can be broken down into several key stages:
1. Conceptual Design
The journey begins with a conceptual design where ideas are mapped out. During this phase, CAD (Computer-Aided Design) software is typically used to create detailed models.
2. Prototyping with 3D Printing
Before moving to injection moulding, many designers will first create a physical prototype using 3D printing. This preliminary model allows for initial testing of form and fit.
3. Mold Creation
Once the prototype has been validated, a mold is manufactured. Depending on the complexity, this can be achieved through various techniques, including CNC machining, EDM (Electrical Discharge Machining), and even 3D printing of metal molds.
4. Injection Moulding
With the mold ready, the injection moulding process can commence. The material is heated until it reaches a molten state, then injected into the mold at high pressure to form the desired shape.
5. Testing and Iteration
After cooling, the part is removed from the mold and subjected to rigorous testing. Feedback is gathered, and necessary adjustments are made either to the design or the manufacturing process.
6. Final Production
Once all iterations have been optimized, the final design can go into full production, leveraging the distinct advantages gained from rapid prototyping.
Applications of Rapid Prototyping Injection Moulding in Metal Fabrication
The versatility of rapid prototyping injection moulding extends to various industries. Here are some applications in metal fabrication:
- Aerospace: Prototyping of engine components and airframe structures that require lightweight, high-strength materials.
- Automotive: Production of parts that undergo rigorous performance testing, including brackets, housings, and clips.
- Medical Devices: Manufacturing custom components for devices like surgical instruments where precision is paramount.
- Consumer Electronics: Quick turnaround of casings and internal components for new gadgets and tech devices.
- Industrial Machinery: Creating complex parts used in heavy machinery that can be tested for durability and functionality.
Benefits of Rapid Prototyping Injection Moulding for Metal Fabricators
Adopting rapid prototyping injection moulding brings forth numerous benefits specifically tailored for metal fabricators:
- Reduced Material Waste: Efficient use of materials leads to a lower ecological footprint, an increasingly important factor in modern manufacturing.
- Streamlined Processes: Integration of rapid prototyping in production workflows can reduce downtime and enhance overall efficiency.
- Collaborative Development: Encourages collaboration among teams by allowing multiple stakeholders to see and test prototypes, fostering innovation and better communication.
- Risk Mitigation: Testing prototypes before full production minimizes the risk of expensive errors during mass production.
- Custom Solutions: Enables metal fabricators to cater to niche markets and customized orders effectively, widening their customer base.
Real-World Case Studies of Success
Many metal fabrication companies have benefited from implementing rapid prototyping injection moulding. Here are some notable examples:
Case Study 1: Aerospace Company
An aerospace manufacturer utilized rapid prototyping for a new aircraft engine component. The initial concept went through multiple iterations within weeks, enabling them to produce a final design that met or exceeded all performance expectations. The reduced time in design allowed for earlier testing phases, ultimately saving the company thousands in development costs.
Case Study 2: Automotive Industry
In the automotive sector, a leading parts supplier adopted rapid prototyping and discovered that they could produce necessary components up to 50% faster than previous methods. The flexibility of injection moulding allowed them to explore new designs, which resulted in lighter and more efficient components, thereby improving vehicle performance.
Case Study 3: Medical Device Manufacturer
A medical device manufacturer turned to rapid prototyping to develop a new surgical tool. The ability to produce quickly and test various iterations allowed them to achieve compliance with industry standards sooner than anticipated, speeding up their product launch timeline.
Conclusion: Embracing the Future of Manufacturing
The adoption of rapid prototyping injection moulding is not merely a trend; it’s an evolution in manufacturing that enhances efficiency, reduces costs, and drives innovation. As the industry continues to advance, metal fabricators must leverage these technologies to stay competitive in an increasingly demanding marketplace.
For those ready to embrace these changes, the benefits of integrating rapid prototyping into your workflow are clear. From improved product quality to shorter lead times, the path forward is filled with opportunities.
To learn more about how your business can benefit from rapid prototyping injection moulding, visit deepmould.net today. Join the ranks of those who are leading the revolution in metal fabrication!